Tampilan Proses Konstruksi Cor Kiln Semen
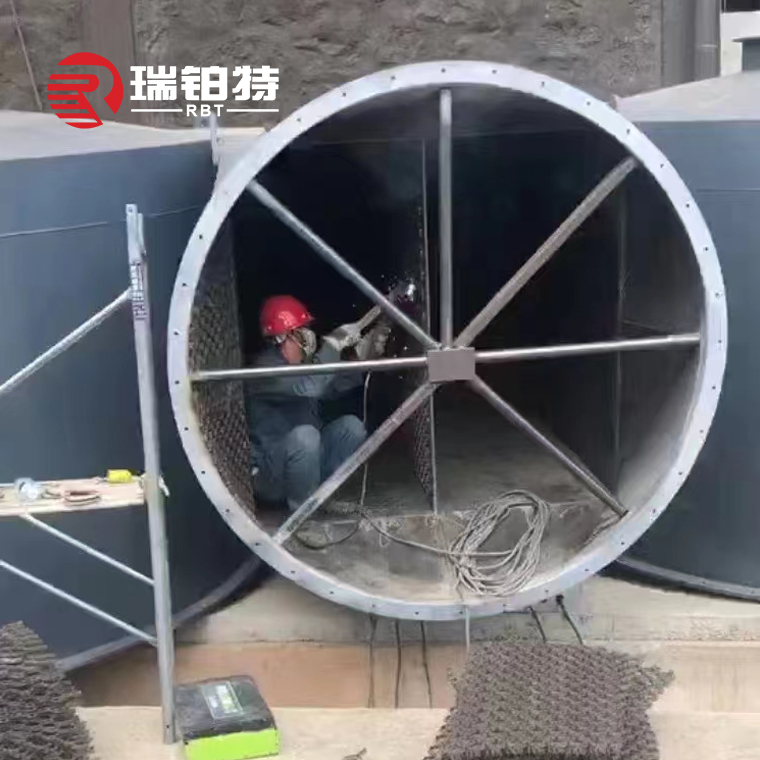
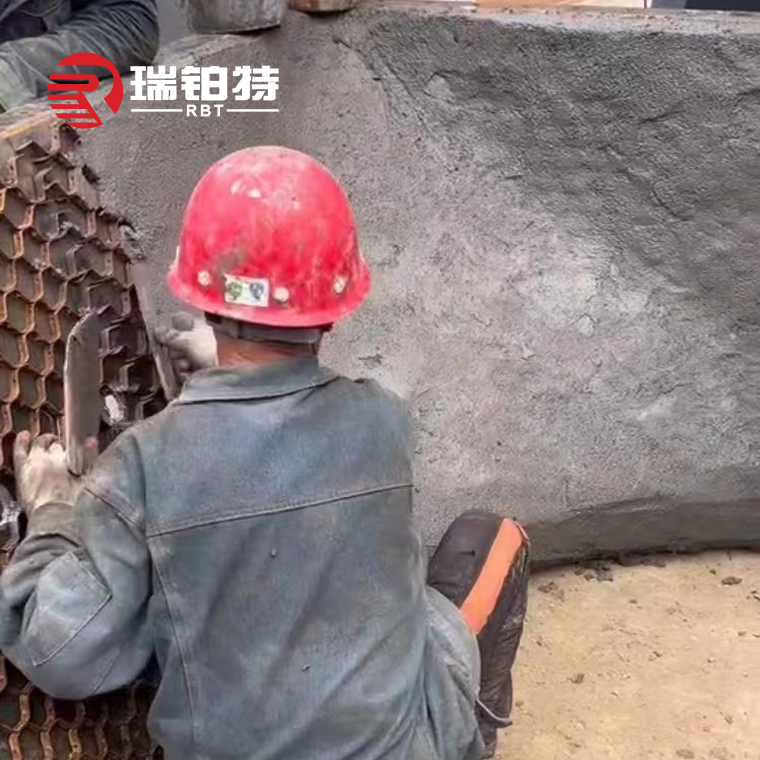
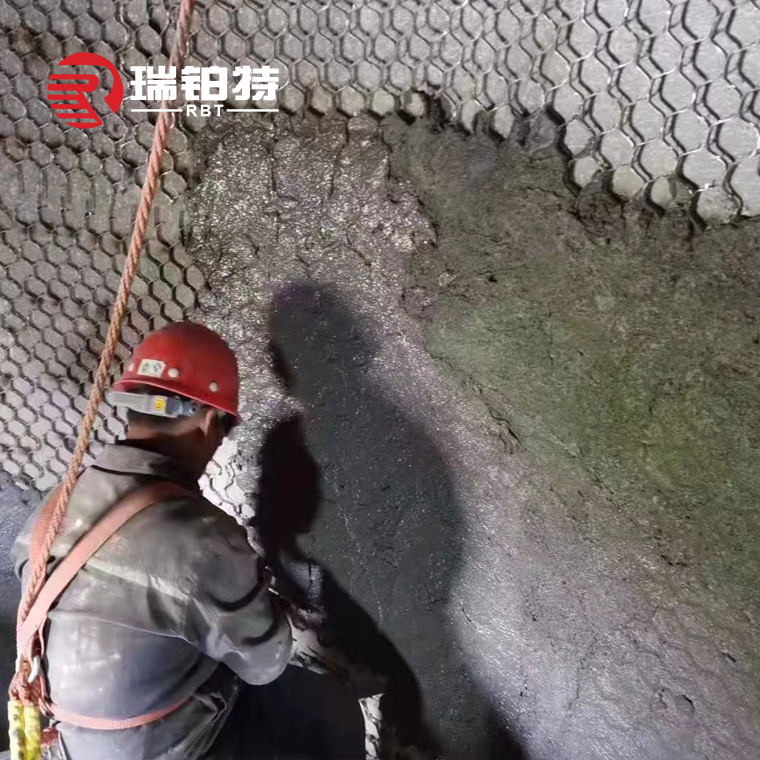
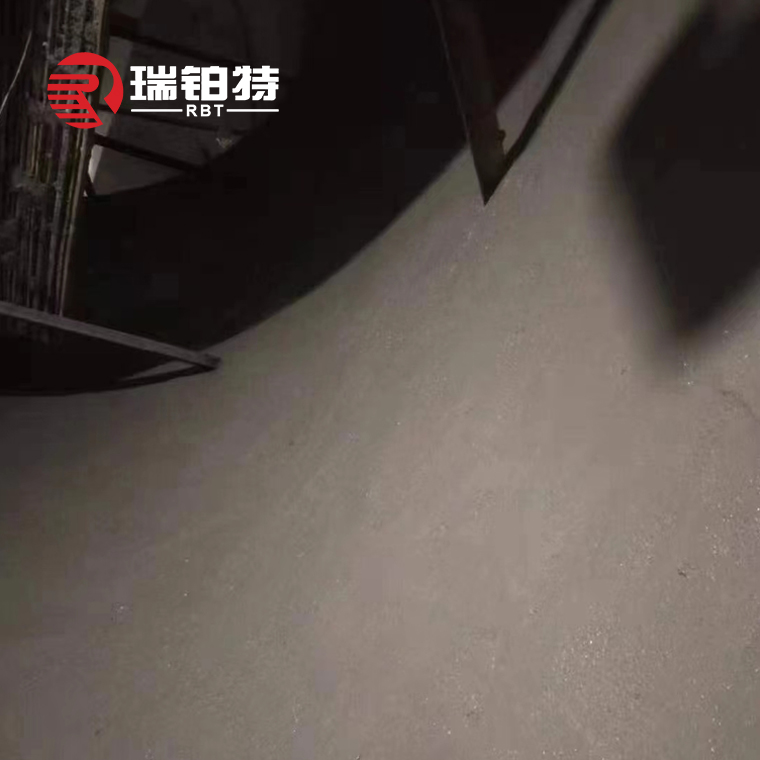
Coran Tahan Api untuk Kiln Putar Semen
1. Castable tahan api yang diperkuat serat baja untuk kiln semen
Castable yang diperkuat serat baja terutama memasukkan serat baja tahan karat tahan panas ke dalam material, sehingga material memiliki kekuatan dan ketahanan guncangan termal yang lebih tinggi, sehingga meningkatkan ketahanan aus dan masa pakai material. Material ini terutama digunakan untuk komponen tahan aus suhu tinggi seperti mulut kiln, mulut umpan, dermaga tahan aus, dan lapisan boiler pembangkit listrik.
2. Castable tahan api semen rendah untuk kiln semen
Castable tahan api semen rendah terutama mencakup castable tahan api alumina tinggi, mullite, dan korundum. Seri produk ini memiliki karakteristik kekuatan tinggi, anti-gores, tahan aus, dan kinerja yang sangat baik. Material ini juga dapat diolah menjadi castable tahan ledakan dengan pembakaran cepat sesuai dengan kebutuhan waktu pembakaran pengguna.
3. Castable tahan alkali berkekuatan tinggi untuk kiln semen
Castable tahan alkali berkekuatan tinggi memiliki ketahanan yang baik terhadap erosi oleh gas alkali dan terak, serta masa pakai yang panjang. Material ini terutama digunakan untuk penutup pintu kiln, tungku dekomposisi, sistem pemanas awal, sistem manajemen, dll., dan lapisan kiln industri lainnya.
Metode konstruksi coran aluminium tinggi semen rendah untuk lapisan kiln putar
Konstruksi coran aluminium tinggi semen rendah untuk lapisan tanur putar memerlukan perhatian khusus pada lima proses berikut:
1. Penentuan sambungan ekspansi
Berdasarkan pengalaman sebelumnya dalam penggunaan coran aluminium tinggi dan semen rendah, sambungan ekspansi merupakan faktor kunci yang memengaruhi masa pakai lapisan coran tanur putar. Sambungan ekspansi selama penuangan lapisan tanur putar ditentukan sebagai berikut:
(1) Sambungan melingkar: bagian 5m, serat silikat aluminium 20mm diapit di antara coran, dan serat dipadatkan setelah ekspansi untuk menahan tekanan ekspansi.
(2) Sambungan datar: Setiap tiga strip coran diapit dengan kayu lapis sedalam 100mm di arah keliling bagian dalam, dan sambungan dibiarkan di ujung kerja, dengan total 6 strip.
(3) Selama penuangan, 25 pin pembuangan digunakan per meter persegi untuk melepaskan sejumlah tegangan ekspansi saat menguras kiln.
2. Penentuan suhu konstruksi
Suhu konstruksi yang sesuai untuk coran aluminium tinggi semen rendah adalah 10-30℃. Jika suhu lingkungan rendah, langkah-langkah berikut harus diambil:
(1) Tutup lingkungan konstruksi di sekitarnya, tambahkan fasilitas pemanas, dan cegah pembekuan secara ketat.
(2) Gunakan air panas pada suhu 35-50℃ (ditentukan oleh getaran uji penuangan di tempat) untuk mencampur material.
3. Pencampuran
Tentukan jumlah campuran sekaligus sesuai dengan kapasitas mixer. Setelah jumlah campuran ditentukan, masukkan material coran dalam kantong dan aditif kemasan kecil dalam kantong ke dalam mixer secara bersamaan. Pertama, nyalakan mixer untuk mencampur kering selama 2-3 menit, lalu tambahkan 4/5 air yang telah ditimbang terlebih dahulu, aduk selama 2-3 menit, lalu tentukan sisa 1/5 air sesuai dengan viskositas lumpur. Setelah tercampur sempurna, lakukan uji tuang, dan jumlah air yang ditambahkan ditentukan dengan mempertimbangkan kondisi getaran dan bubur. Setelah jumlah air yang ditambahkan ditentukan, hal tersebut harus dikontrol secara ketat. Sambil memastikan bubur dapat digetarkan, air harus ditambahkan sesedikit mungkin (jumlah penambahan air referensi untuk coran ini adalah 5,5%-6,2%).
4. Konstruksi
Waktu pengerjaan coran aluminium tinggi semen rendah adalah sekitar 30 menit. Material yang telah dikeringkan atau dipadatkan tidak boleh dicampur dengan air dan harus dibuang. Gunakan batang getar untuk menggetarkan dan mencapai pemadatan bubur. Batang getar harus disisihkan untuk mencegah batang cadangan aktif ketika batang getar rusak.
Konstruksi material cor harus dilakukan dalam bentuk strip di sepanjang sumbu tanur putar. Sebelum setiap pengecoran strip, permukaan konstruksi harus dibersihkan dan tidak boleh ada debu, terak las, dan kotoran lainnya yang tertinggal. Pada saat yang sama, periksa apakah pengelasan jangkar dan perawatan cat aspal permukaan sudah terpasang. Jika tidak, tindakan perbaikan harus diambil.
Pada konstruksi strip, konstruksi badan pengecoran strip harus dituang secara terbuka dari ujung kiln hingga kepala kiln di bagian bawah badan kiln. Penyanggaan templat harus dilakukan di antara angkur dan pelat baja. Pelat baja dan angkur tersebut dilapisi dengan balok kayu. Bekisting penyangga memiliki tinggi 220 mm, lebar 620 mm, panjang 4-5 m, dan sudut tengah 22,5°.
Pembuatan badan pengecoran kedua harus dilakukan setelah strip akhirnya terpasang dan cetakan dilepas. Di satu sisi, cetakan berbentuk busur digunakan untuk menutup pengecoran dari kepala kiln hingga ekor kiln. Sisanya serupa.
Saat material cor digetarkan, lumpur campuran harus ditambahkan ke dalam cetakan ban sambil digetarkan. Waktu getaran harus dikontrol agar tidak ada gelembung yang terlihat pada permukaan bodi cor. Waktu pelepasan cetakan harus ditentukan oleh suhu lingkungan di lokasi konstruksi. Penting untuk memastikan bahwa pelepasan cetakan dilakukan setelah material cor akhirnya mengeras dan memiliki kekuatan tertentu.
5. Pemanggangan lapisan
Kualitas pembakaran lapisan tanur putar secara langsung memengaruhi masa pakai lapisan tersebut. Dalam proses pembakaran sebelumnya, karena kurangnya pengalaman yang matang dan metode yang baik, metode injeksi minyak berat untuk pembakaran digunakan dalam proses pembakaran suhu rendah, suhu sedang, dan suhu tinggi. Suhu sulit dikontrol: ketika suhu perlu dikontrol di bawah 150℃, minyak berat tidak mudah terbakar; ketika suhu lebih tinggi dari 150℃, kecepatan pemanasan terlalu cepat, dan distribusi suhu di tanur sangat tidak merata. Suhu lapisan tempat minyak berat dibakar sekitar 350~500℃ lebih tinggi, sementara suhu bagian lainnya rendah. Dengan cara ini, lapisan mudah pecah (lapisan cor sebelumnya pecah selama proses pembakaran), yang memengaruhi masa pakai lapisan.
Waktu posting: 10-Jul-2024